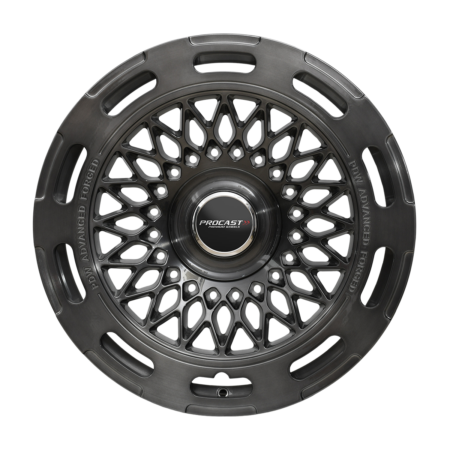
Procast is a global leader in forged wheel manufacturing. We’re proud to be one of the few companies with a legacy of serving the world top brands for over 4 decades. Our slogan, “Supreme Craftsmanship, Unparalleled Performance,” captures the essence of our commitment to excellence and the superior quality of our forged wheels.
Supreme Craftsmanship, Unparalleled Performance
We provide one-piece and two-piece forged rims, and support customization of styles and colors. More than that, We have an extra advantage that sets us apart from the competition: low minimum order quantities.
The term ‘forged’ refers to making an alloy wheel by forcing a raw metal block into shape with tremendous pressure. Our forging craftsmanship sets us apart from the competition. From the programming to the forging process to the CNC milling, engraving and quality control- each step in our production is a blend of innovation, precision and pursuit of perfection.
Regarding forging, crafting wheels of high-quality aluminum alloy, is a multi-stage process.
The first and foremost step in forged wheel construction is the careful forging of wheel blanks from the selected billet of high-quality aluminum alloy. While maintaining an optimal temperature, the billet is subjected to extreme pressure to form the wheel’s basic structure. At Procast, we apply 8,000 – 10,000 tons of pressure to compress the billet into a disk.
Then, the disk is pressed within a unique matrix, forming a narrow wheel blank. For designer forged wheels, specialized forging tools are used to bring artistic precision to the wheel’s design.
After the forging process, the wheel blank undergoes a carefully controlled heating phase. This elongation of the wheel blank is done through three rotating rollers. A pressure of 10t is applied to elongate the wheel blank in the desired rim width. Procast forms an unusually thin rim of 2.25 mm thickness on the finished wheel in the cutting-edge technique.
To further redefine material’s microstructure, the wheel blank undergoes a strong heating phase known as solution annealing. Then the blank is subjected to rapid cooling upto 70°C to harden the molecular structure.
After the quenching, the wheel blank endures artificial aging, allowing the blank to rest at a pre-defined temperature for a longer period, so the material stabilizes. At Procast, the heat treatment process is completed in 840 minutes under controlled conditions to achieve the desired quality of the product.
Procast uses mechanical CNC (Computer Numerical Control) machining to ensures precision and consistency, laying the groundwork for the intricate design of the wheel. The latest 5-axis CNC machines are used for carefully milling the actual wheel design with all of its features.
After milling, all wheel blanks undergo runout checks to ensure that the runout is within the standard limit. Finally, the finishing process involves deburring and blasting the wheel blank through an automated process.
The last stage in the forged wheels construction is lacquer finish. After pre-tretament of the blank, base powder is applied to the wheel surface, matching the desired color requirements.
For applying the paint layer, Procast uses electrostatic coating and compressed air spraying on the powder-coated wheel blank so it is distributed evenly. Then, a final clear lacquer coat is applied, serving as a protective layer. A final quality check is done before packaging to eliminate any errors and ensure the high quality.
As a wheel manufacturer, Procast prioritizes flexible customization. With advanced equipment and a skilled team, we tailor wheel rims to meet unique requirements of each customer. From colors to styles, we provide personalized solutions with low minimum order quantities, ensuring accessibility and customer satisfaction.
The flow-forming process provides integral strength to the wheel, so less material is required to provide the same strength as other methods. This lets you maximize your investment by finding the middle ground between performance and resource efficiency.
Our forged wheels undergo a 12-hour heat treatment processs. The initial solution heat treatment and natural aging provides a foundation of strength. The subsequent artificial aging in a high-temperature furnace enhances the alloys mechanical properties. This leads to a strengthened and hardened wheel.
Each of our forged wheels undergoes a rigorous 100% balancing test, ensuring you experience stable-steering, improved tire longevity and a vibration-free ride. We use specialized equipment to measure the distribution of weight around the wheel and ensure it perfectly balanced
After achieving perfect balance, we subject each wheel to not just one, but two rigorous air-leakage tests, providing a comprehensive evaluation of their airtightness. Only wheels that are verified as airtight are passed to thee next stage.
Our three-story conveyor painting line ensures your wheels have a uniform and smooth finish. Our meticulously designed painting coating line features five production lines, with three incorporating fully robotic automatic spray systems equipped with advanced sensor detectors.
Our imported machinery ensures precision craftsmanship in our wheels. Our CNC operations boast efficiency with 14 stations for op1/op2, another 14 for op3, and an additional 8 dedicated to machine facing. The versatile machines can handle wheel sizes ranging from 8” to 26”.
For brands and agents seeking uniqueness in their product lines, Procast offers a gateway to innovation. We support customized one-piece forged wheels and two-piece forged wheels. Our professional design team sets the trends instead of just following them.
Procast monoblock/one-piece forged wheels are the epitome of simplicity and innovation. Crafted from a single piece of premium 6061-T6 aluminum alloy, these wheels redefine lightweight performance and affordability. If you want the stiffest, strongest, and lightest wheel possible, you want Procast Monoblock Wheels.
Procast 2-piece fastened wheels combine heightened strength with customization. These high-quality forged wheels are light, strong and give supreme performance. The two-piece construction enhances structural integrity, providing a robust solution for heavy-duty applications. Tailor your wheels with a range of finishes and design options, reflecting your brand’s unique identity.
Procast three-piece forged wheels are the pinnacle of precision and customization . Tailor our custom three-piece wheels to your liking – from finishes to widths. The modular design of our three-piece wheels allows for dynamic weight distribution, optimizes performance and ensures stability across different load capacities for various vehicles.
We accept 2 models load in one container at the most.
Cartons with steel frame inside. We can also put your logo on the cartons.
Yes, we welcome OEM and ODM order.
Are you prepared to enjoy the benefits of PROCAST? Contact us now to learn more about our offerings and how we can help you grow your company.
868#, Dayan Road, Linjiang Industrial Zone, Wucheng District, Jinhua City, Zhejiang China, 321000
Johnson@procastwheel.com(for manufacturing enquiries only)
+86 182 5799 2529